Blog
Every year the Fab Lab Barcelona organises and runs an academy as a form of knowledge exchange based around a series of projects that are carried out by Distributed Design Platform members in line with distributed design principles. This year’s program was the Crafts TECH 2021 – Maker to Market Accelerator, carried out online in a distributed manner and co-organized by Artesania Catalunya of the Consorci de Comerç, Artesania i Moda (CCAM) of the Generalitat de Catalunya. Crafts TECH was based around upskilling and empowering designers and makers working in digital fabrication by equipping them with a set of tools to help them to enter new and emerging markets.
Crafts TECH 2021 had 33 participants, each of whom brought their own project. Below we will present you three of them. The training took place online from the 4th to the 22nd of October 2021.
This year, the goal was for participants to deepen their entrepreneurial knowledge and provide inspiration and guidance on how to access new markets and view their own discipline from different perspectives. The program addressed the last phase of product development, in what we have called “Maker to Market”.
The Crafts TECH 2021 – Maker to Market Accelerator provided the participants the opportunity to expand their knowledge and practice distributed design principles in a hands-on interactive workshop environment. Having participants coming from the Distributed Design Platform as well as from the open call created an environment for knowledge exchange and collaboration that enabled varying perspectives on what design means in different contexts whilst being able to strengthen their personal network.
Structure
Week 1
October 4: Welcome and presentation of the program. Opening Session
October 5: Project Sustainability & Business Models. Alessandra Schmidt.
October 6: Digital Design. Kate Armstrong.
October 7: Communication. Marcel Rodriguez.
Week 2
October 11: Knowledge Transfer focused on Artisans.
October 15: Knowledge Transfer focused on Makers.
Week 3
October 19: Collaboration and digital design. Open questions.
October 20: Communication. Open questions.
October 21: Financing and sustainability of the project. Open questions.
October 22: Final presentations.
Interview with participant Boglárka PITENYÁK
Can you introduce your project?
Project: “FUTURA MATERIUM”
Presumably, in the Post-Covid age, naturalness and sustainability become defining concepts. My project aims to use natural materials that are unused or by-products and compare them with existing industrial technologies. I use citrus peels, leather waste, bone- and skin glue, agar-agar, gelatines, plant-based glycerine, water, coffee grind, and used tea leaves to make biobased, biodegradable leather-like materials. I use molding, lathe machines, natural gluing to form and work the materials. Firstly I made summer bags, small cases from the materials, so now they could be a product also. Now they are durable, slightly flexible, water-resistant, opaque, or easily colorable. Used materials are by-products, “raw material” and production costs are low with minimal energy use. In my opinion, it can change the method of how we make fashion accessories and how to use them. It will be an alternative solution for more sustainable fast-fashion products and bring a new experience for customers.
Project: “Helyi” (it means local in Hungarian)
This project is a small StartUp plan for supporting young Hungarian fashion designers to start their career. It is not another showroom or brand. It is a platform where they can sell designs, tailoring patterns in digital form. It gives a chance for conscious customers to get original designer products locally made that they can make themselves or with local makers, tailors, dressmakers from their fabrics or locally buy and made fabrics. With this method, we could treat textile materials as an energy resource, and use them in several lifecycles. The customers will get much more personalized, quality, durable, long-lasting design products.
Which materials are used in your project?
Futura Materium: skin glue, bone glue, plant-based glycerine, used tea leaves, leather waste, coffee grind, citrus peels, dry flowers, agar-agar, animal-based gelatine, pigments, water
Which machines, techniques, and technologies are used in your project?
Helyi: Only digital solutions, such as 3D rendered designs, Adobe programs (maybe the designers will use some paper or natural materials for modeling
Used machines, technologies: Lathe, mold forms(soon they can make with CNC milling or 3D printing), brush gluing, punching, lacing, folding
Interview with participant Louis Rose about her project Local Discontinuity
Can you introduce your project?
This project aims at giving credibility to local scenarios of circular economy based on the upcycling of organic resources. While a previous phase investigated the challenges of collecting bio waste from restaurants, transforming it into usable bio-based materials and proposing those materials to the public, I then used the DDMP Summer School to dive into the technical dimension of building the required tooling: a bio-press.
Locally produced from restaurants and cafes’ byproducts (coffee ground, stale bread, shells, peels…), bio-based materials represent an attractive and biodegradable alternative to single use plastic packaging. The press – through heat and pressure – creates the necessary conditions to condense and polymerize the mix, and will bring me empirical knowledge and proof of concept before envisioning key partnerships.
Stemming from the current surge in interest towards bio-based materials and the Circular Economy, Local Discontinuity – as its name suggests – advocates for the creation of disruptive, local and circular initiatives. Extracting knowledge from existing distributed resources (Beyond Plastic, Materiom, DDMP, etc…), the project strives to bring together the behavioral – are people willing to change? – and structural – do people have the option to change? – components of a transition to more circular and responsible societies.
Which materials and machines are used in your project?
There are at least two distinct elements, or phases, within the project, each of them making use of very different techniques and materials:
The part I am dealing with right now is the building of the press, the necessary tooling to shape bio-based materials. This phase calls for the use of metal and wood, and for the technologies associated with the work of those materials: drilling, threading, welding (if that was available in the makerspace I’m using), threading, CNCing…
The second phase will be about putting the press to the test, as the main tooling of the bio-based materials shaping process: those materials comprise mixes of coffee ground, peels, shells, sawdust, stale bread … and more. Here, the needed equipment includes a drier and a blender to process the raw resource.
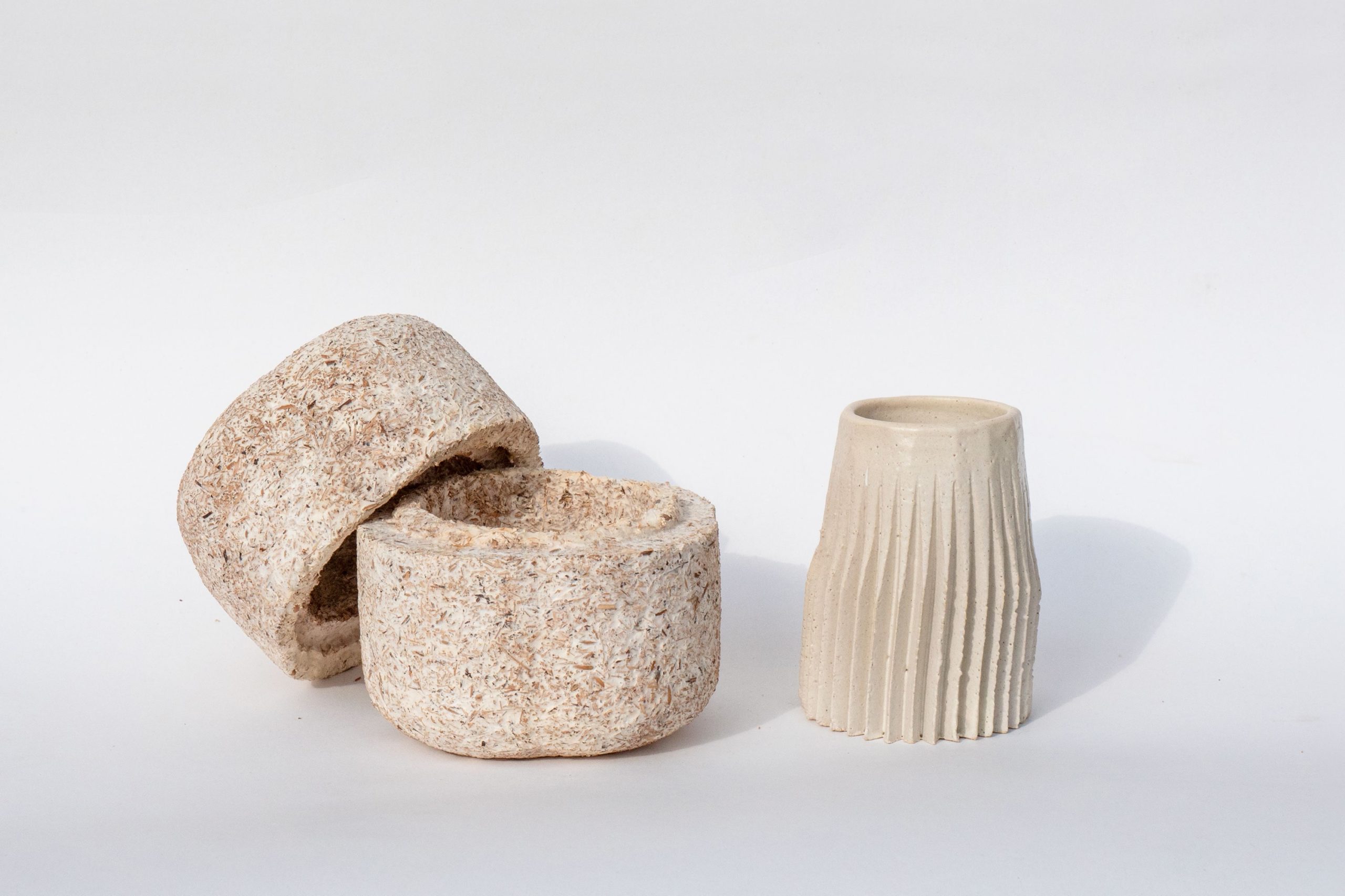
Interview with participant Rob Oblak
Can you introduce your project?
I’m currently working in 3 directions that consider Distributed Design: 1. ceramic workshop Levo where I produce ceramic pieces with the use of 3D printed molds (www.saltodionys.com), 2. production space (www.krater.si) where I manage the development of products from biomaterials like mycelium, paper pulp from invasive species and local clay products, and 3. I’m managing a ceramic and glass department of the new-coming biggest production center in Slovenia called ROG (https://roglab.si/en/), that will have all the latest technology equipment (also biolab, 3D print, electronics, wood, metal, textile depts etc.) This will open in 2025.
I’m mainly interested in small-scale craft production that considers machines as 1-person use, like micro-initiatives, DIY and DIT methods, alternative economies and social engagements of local communities that evolve from this mode of production. I work with 3D printing, CNC and laser-cut techniques, mainly for tool manufacturing that help artists and designers with their work. I run public workshops and occasional TA-ing on the local Arts and Design Academy in Ljubljana / Slovenia.
Which materials are used in your project?
Ceramics, local clay, paper pulp (invasive species), wood, PLA (3D print), mycelium/mushrooms and other biocomposites
Which machines, techniques, and technologies are used in your project?
3D printing, extruding, laser cut, CNC, mold-making, local clay extraction
The event is part of the Creative Europe program of the European Union and #Talent_jove 2019-2022 program promoted by Artesania Catalunya of the Consorci de Comerç, Artesania i Moda (CCAM) of the Generalitat de Catalunya. CCAM provides new tools to the craftsmanship sector and also fosters new business and production models.
Program by: Distributed Design Platform
Co-organized by: Fab Lab Barcelona | CCAM | Generalitat