BioFan
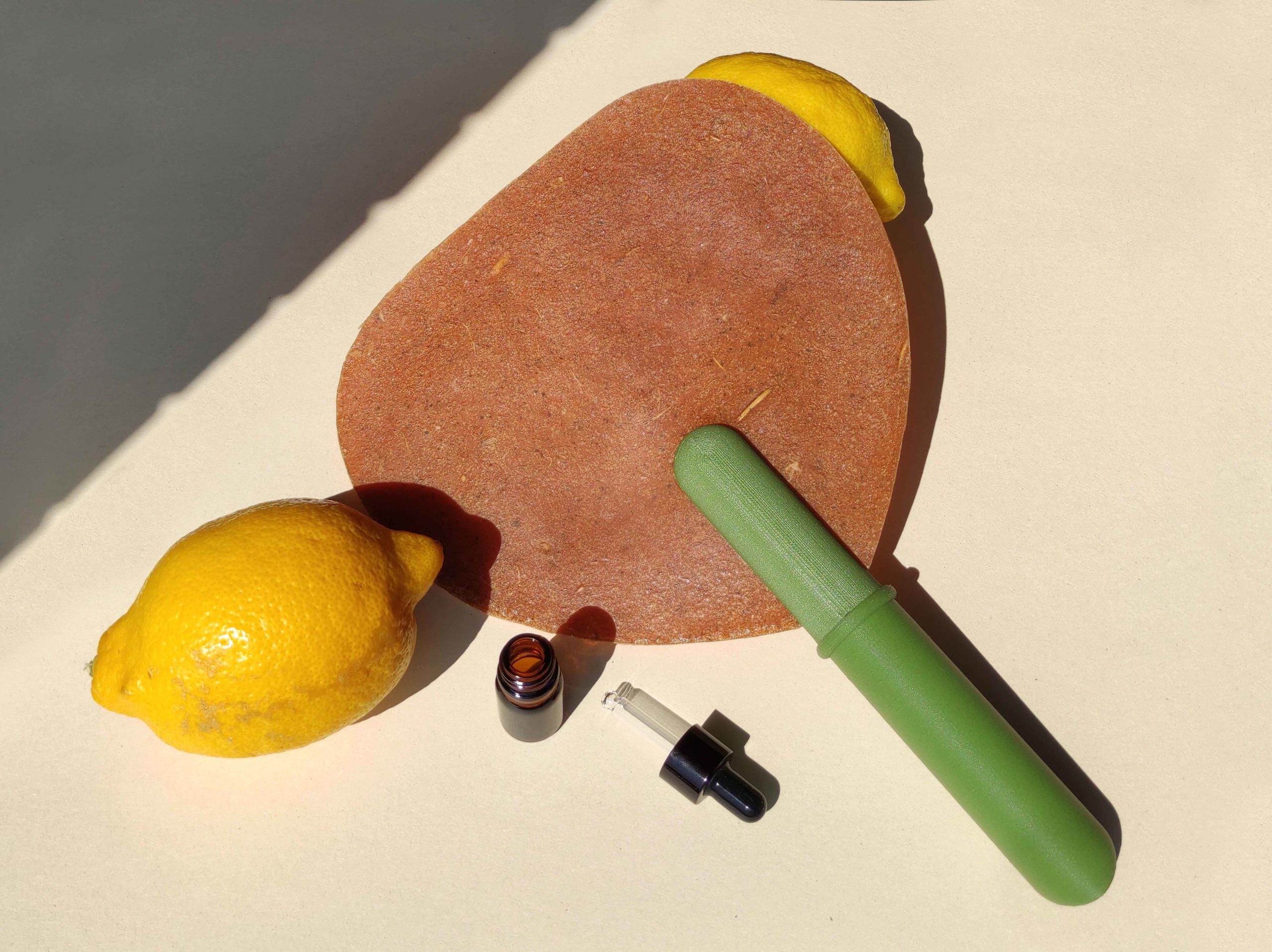
Useful information
- Team members
- Greta Dalessandro Alberto Ghirardello
- Country
- Italy
- Keywords
- new materials biodegradable foodwaste 3Dprinting DIY biomaterials materialresearch biodesign zerowastedesign biofabrication customization 3Dprinter custom3Dprint
Short Description
BioFan is an open-source fan made of lemon peel-based biomaterial and 3D printed hemp-based plastic.
Detailed Description
The strong bond with nature was a source of inspiration for the choice of material for BioFan’s flat surface: a mixture of lemon peel, mint leaves, gelatin and glycerin. A coherent formula both for the seasonal origin of the ingredients and for the desire to use organic waste material as a base for bioplastic, characterizing its texture, flexibility and odor. At last it allows it to be replaced by simply produce a new piece if it gets damaged, without waste and with zero impact on the environment. The handle/ clamp is made entirely in 3Dprinted hemp filament, and the hinge and closure system has been carefully studied to offer a practical and stable fixing of the biomaterial part, which adapts to the consistency and to the variable thickness of the DIY result and that makes it quick to replace in case of breakage. The bottom of the handle also houses a dropper bottle, useful to enrich the bioplastic with essential oils so that when you fan yourself you also diffuse a good scent.
Project Details
- Does your design support sustainable production, embodying circular or regenerative design practices?
Yes, the project was designed and manufactured following a totally sustainable perspective. First of all, since the product has no secondary processing (painting, coating, gluing, etc.) it presents itself with the natural finish of the materials it is made of, making the materials the real protagonists of the project and elevating them to a strongly connotating aesthetic feature.??The biomaterial part is easily replicable and replaceable in case of breakage or decay following the same recipe, and the part to be replaced is 100% compostable, being made up only of food waste, gelatin and glycerin.??The 3D printed part has been designed to be free of irreversible joints, making it possible to reprint each single piece in case of breakage. In addition, every single part has been designed to be printed without the aid of supports, obtaining zero plastic material waste even in the printing process.
- Does your design use principles of distribution and open source?
Yes, BioFan is the pilot project of a series of products / kits with the aim to promote and encourage a concrete and intuitive use of DIY biomaterials in daily life with the help of 3D printing technology.. Simple but above all hybrid products with a strong customization component, both for the 3D printed part but above all for the bioplastic part, which in fact does not need to be replicated in a laboratory. On the contrary, it can be easily produced directly at home by following the simple instructions for preparation and can be adjusted and varied, just like a culinary recipe.??BioFan, together with the other projects under development, will soon be disclosed as open source designs, letting the 3D files for the printing of the hard parts available to the public for free, together with the recipe / tutorial for the domestic realization of the biomaterial part. Both of its cores (3D printing and DIY biomaterial) offer a high degree of customization: the first allows the end user to design the aesthetic shape they prefer for the handle, keeping as the only constraint the internal hollow volume suitable for housing the dropper bottle; the second allows to have the shape of the flat part as desired, as well as to customize color, texture and scent simply by using different ingredients / food waste to obtain a wide range of different aesthetic results adaptable to every need.
- Does your design promote awareness of responsible design and consumption?
Yes, BioFan also wants to be a tool to raise awareness of the responsible use of resources, as it consists largely of food waste and easily replaceable parts, extending the life of the product and significantly reducing its obsolescence. Furthermore, being totally open source, it allows it to free the production from a specific location constrains and to be manufactured anywhere in the world through a simple, widespread and accessible FFF / FDM desktop 3D printing technology and resources for the realization of the DIY biomaterial available in any kitchen.