In times of COVID-19, distributed design had quickly become our reality out of necessity. Fab Labs and maker spaces started distributing machines, companies started collaborating, and designers worldwide opened their processes to rapidly design, and many individuals wanted to help and innovate health and wellbeing equipment in response to the crisis on a global scale. For one, distributed design and digital fabrication can help overcome supply problems in a crisis. For effectively supporting the fight against COVID-19, you need to know, however, where your help really has an impact on medical needs.
Quick Response with Local Production
Paulien Melis, programme developer at Amsterdam-based research institute Waag, works at MakeHealth Lab — a programme where they invite people with healthcare questions, healthcare professionals, makers and designers to co-design and co-develop personalised healthcare solutions. Current markets are only serving a certain amount of people, but some have special needs as the materials don’t fit. That’s where the capacity of makers and designers comes in. By matching them with people with needs and the know-how to use it, MakeHealth Lab facilitates medical innovation on a local scale.
When COVID-19 hit Europe, MakeHealth Lab focused on the production of medical face shields. According to Paulien, it’s critical that medical expertise is involved. “You absolutely need to make sure that it is validated and full proof. Otherwise, you create a fake sense of security and maybe even do more damage by spreading the disease instead of preventing it.” While MakeHealth wanted to push co-designed and co-produced solutions on a European and even global scale via networks like www.carebles.org, it was hard gathering insights from health care professionals in these times. “They were all needed for acute care and medical support related to the virus”, Paulien adds. “It’s amazing to see how fast the maker community responded— bringing their design capabilities, skillset, and power to the table. But designers are no health professionals— validation with research institutes, universities, or healthcare workers is crucial to see if the design is progressing in the best possible way.”
Finding your Network
Not every maker or designer has a network like that. Where do you find people that can help you validate your design? “There are organisations like TNO (Dutch Organisations for Applied Scientific Research) that can help you, but sometimes it’s also the healthcare professionals that reach out because they see a need”, Paulien says. “For example, my dentist is producing and developing a mouth mask together with a social lab for sustainist design.” There are several ways for collaborating and finding each other, the advice is to take the effort to find that match, and make that search an integral part of your design process.
One of the things Waag did was setting up a shop with laser cutted transparent face shields that can be disinfected. They used files are from a validated design from Belgium-based Makers against Corona, where it’s used in hospitals. That’s the power of distributed design: instead of producing in Belgium and shipping it to the Netherlands, local production facilities can reach out to local organisations that facilitate elderly care, home care, or other people that need personal safety measures. “Looking at a larger perspective”, adds Paulien, “you are also preventing becoming dependent on factories in say China, risking waiting for a shipment that needs to be returned cause it doesn’t fit local validations.” Distributed design offers short lines and more possibilities in the production and accessibility of equipment.
Pieter van Boheemen, hacker, engineer, and researcher at Rathenau Institute is one of the makers working together with Waag. Pieter started working on PPE based on a snorkeling mask (Snorkel Mask 4 Life, 2020). The mask itself is available at a well known French sporting goods retailer. Adding a 3D-printed connector and a P3 filter, it should protect you from catching the virus. Pieter’s sister, who is a doctor working at a hospital and indicated supplies were soon running low, was his motivation to start the project. She showed him a picture of a colleague wearing a similar mask and asked her brother to make her one too. Pieter found online communities with researchers, makers, and designers from Chile, Italy, Croatia, the United States, and many more countries working on designs together. In the Netherlands, he connected with many local makers through a Whatsapp group.” Basically, I reached out to everybody that I know that has some connection to personal protection”, says Pieter. “That’s how I also found someone that could validate what we were actually doing, so he started testing the models in a properly certified setting and the results have been what we were hoping for.”
Catering Local Needs
Pieter is using 3D prints for the connectors, which are sufficient for prototypes and single-use. For sterilisable (and therefore reusable) connectors, it is better to produce the connectors by injection molding. The design for the connector is open-source and published on Thingiverse. He published two different files, one for the connection to the mask (from Decathlon) and one for the connection to the filter (RD40). That’s also one of the beauties of distributed design; it makes customisation on a large scale possible.
It’s also what Erik Cederberg, lead engineer at Stockholm based 3DVerkstan and co-founder of Makers of Sweden figured out. Erik and his team designed a quick to print and easy to assemble protective visor, consisting of a frame for holding standard sized plastic sheets. The plastic shield can be made out of any semi-stiff plastic sheet between 0.1 and 1mm, including overhead film, cover sheets for binding machines, etc, as long as it is available in a suitable format. Soon, architecture firms, design studios and maker labs across the world were using their 3D-printers and laser cutters to make thousands of copies of his clinically tested #3DVFaceshield, which are being delivered to hospitals for distribution to frontline medical staff amid shortages of the safety devices. Due to the difference in standards for hole punchers (the ones you get in an office supply store), Erik’s open-source design is available in three versions: for Sweden, Europe, and North-America.
“We felt the need to come up with a design that was effective, fast to print, and can be manufactured in large quantities. We expected it would take a few more weeks before the medical supply industry would be able to start up the process of local production.
To meet short term demand, distributed design and manufacturing would be really useful so we started designing quite iteratively with the help of professionals working at one of the larger hospitals in Stockholm.”
Within 72 hours and many prototypes, they came up with publishable files. Official governmental validation in Sweden costs about eight thousand euros and takes three weeks, so they decided to do an internal validation with five different hospitals instead. After positive results, each local healthcare region independently (Sweden has a decentralised healthcare system where the 21 regions themselves establish principles and guidelines and set the political agenda for health and medical care) decided to take the responsibility for distribution and provided local hospitals with the face shields. By mid-April— as far as Erik can oversee— Swedish volunteers already printed at least 70,000 copies of the design. worldwide numbers are hard to track.
The most impressive story though came from Ghana, where a local surgeon reached out to Erik with the message asking him to send one visor so he could ask a local plastic factory to copy the design. Erik remotely connected him with a local one-man factory he found online who’s building 3D-printers for the West African market. Together, they were able to set up a print farm for the hospital. “What made a huge difference is when lots of maker groups and even companies started pivoting towards injection molding with this design. There are at least seven factories that I know of that are doing that now. Two of them are located in India and they can produce 70,000 copies a day that way.”
Customised Design
Erik wanted to design something that could be made with locally available materials. “Where can we find transparent plastic in large quantities that people can get easily? Office supply stores! Sheets, overhead film, rapport covers, basically everything that is A4 shaped and transparent enough”, says Erik. “The next question is: how do you fasten that on a 3D-printed part? You could use a laser cutter for that but we felt we needed a more common tool.” Hole punchers are something that every household, office, or hospital has available. However, because the dimensions of hole punchers differ worldwide (for example, Sweden has a four-hole national standard that is almost exclusively used), multiple designs were needed. “I have definitely learned way more about hole punchers than I knew before”, Erik answers with a smile. To test the design for the North-American market, he called in a favour from an American friend for help. “In the US, Canada, and in a part of Mexico and the Philippines, a three-hole standard is widely used. The first test showed three holes are not strong enough to hold the sheet, so we designed a frame with six holders which means you have to punch the sheet twice.” In the design, Erik took into account that it is suitable for different head sizes by giving an option to add a rubber band for optimal security.
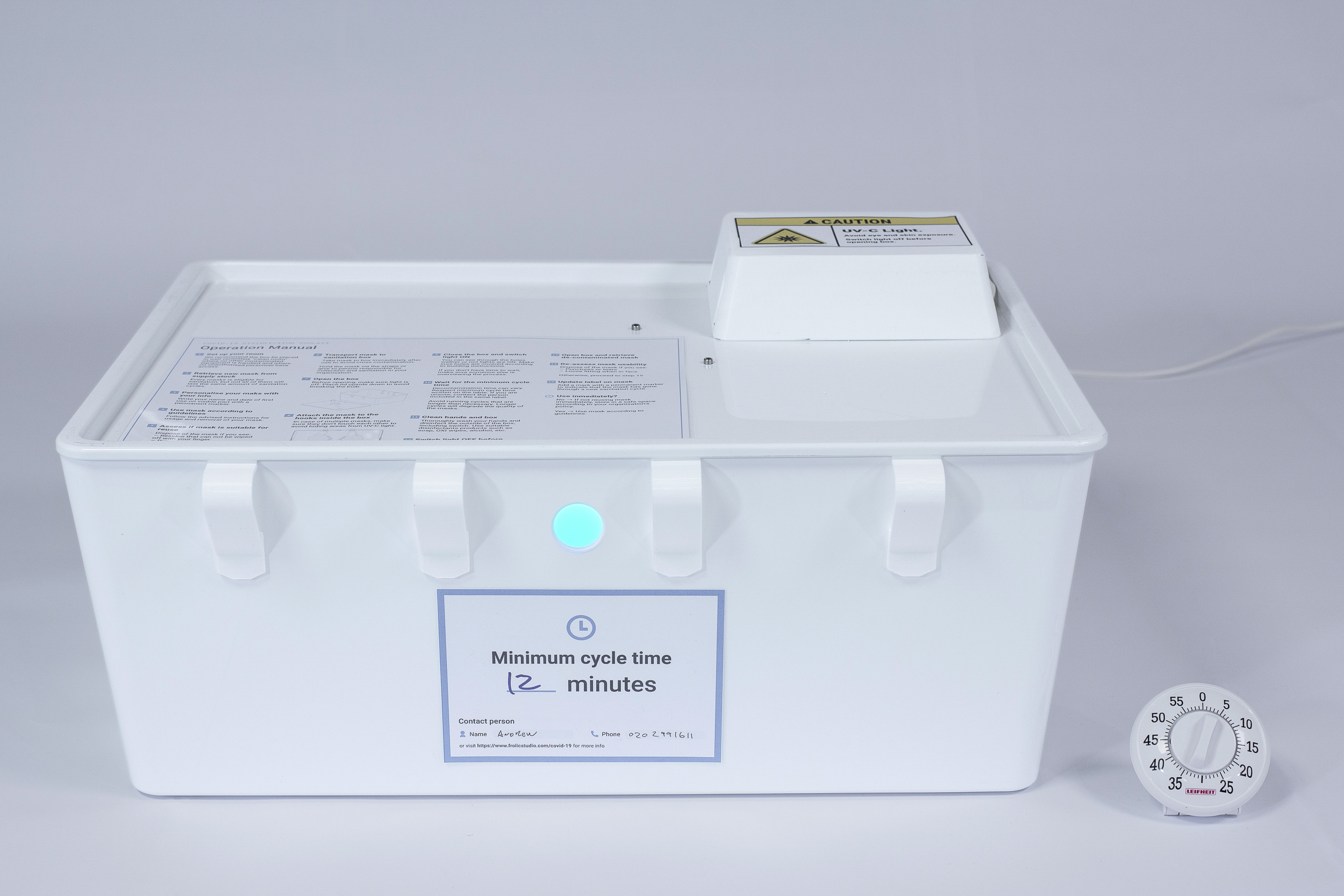
Co-creation and Validation
Amsterdam-based FROLIC studio also wanted to put their resources and network towards COVID-19 critical challenges. Rather than adding stuff to what the maker community already was successfully doing— making more personal protective equipment— the team of multidisciplinary designers decided to focus more on recycling as a way to handle the scarcity of equipment based on knowledge gained from conducting in-depth research and interviews with healthcare workers and organisations. Was it technically possible to design something that would work for this particular case? Medical research published by an American University gave them the confidence to push through designing a COVID-19 Decontamination Kit. “Validation in design means many things”, says Ismael Velo Feijoo, product designer at FROLIC. “One thing is testing if the solution is actually adding something. For that, we set up a design research process parallel to the development of the device. We needed to dive into the context, which is a strategy you always want to take.” The team designed the DIY decontamination toolkit based on IKEA’s KUGGIS box, which can be put together for around fifty euros and uses UV-C light to sterilise and extend the life of protective face masks. “When we had the first prototype ready, we found a lab in Germany who was not only capable but also willing to help us. That happened all in the first week of designing.”
Availability of Materials
“The minimum decontamination time is the result of a few parameters”, Ismael explains. “It depends, for example, on the size of the box and the power your lamp offers, so we implemented a simple online calculator where you can fill in these different parameters and it will tell you an estimation of the time you should leave the personal protective equipment inside, which is already several times higher than what would already be sufficient but with these things you want to be extra sure.” For the kit, you could use any available storage box. But just like Erik, Ismael and his team were also questioning which supplier is almost always present . “In our case, we figured that was IKEA”, Ismael answers. “The box is relatively cheap to afford and fits well, it has the perfect shape. Another reason is that we needed it to look better than the average GitHub internet tutorial.
“It should not only work well, but it should by its look communicate trust as well, that it is something reliable. Technically, it would also work with a cardboard box with tape around it.”
Taking a Deep Dive
Just like Paulien experienced the lack of availability of health care professionals for the design process, also FROLIC had to try extra hard. Due to COVID-19, they couldn’t physically show up to the places where their design might be deployed. Instead, they set up a series of (online) interviews that gave them insights from the practitioners working in the first line of action. “The challenge was to gather all this information and also process it so we would end up with a good picture of all the needs and wants in such a short amount of time.”This was made possible with the help of volunteers who came out to offer their skills after an online call-out, in addition to dozens of medical healthcare workers and people on the frontline who answered their call and shared their stories. “Although it was important to understand the user interaction with the product, this also helped us with the details to make it really powerful, like how you handle the type of advice you give, or the safety considerations, all that wouldn’t be possible without this research. Paradoxically, the COVID-19 decontamination kit is a result of taking a step back, and not responding immediately to what was surfacing online and around us”, Ismael adds.
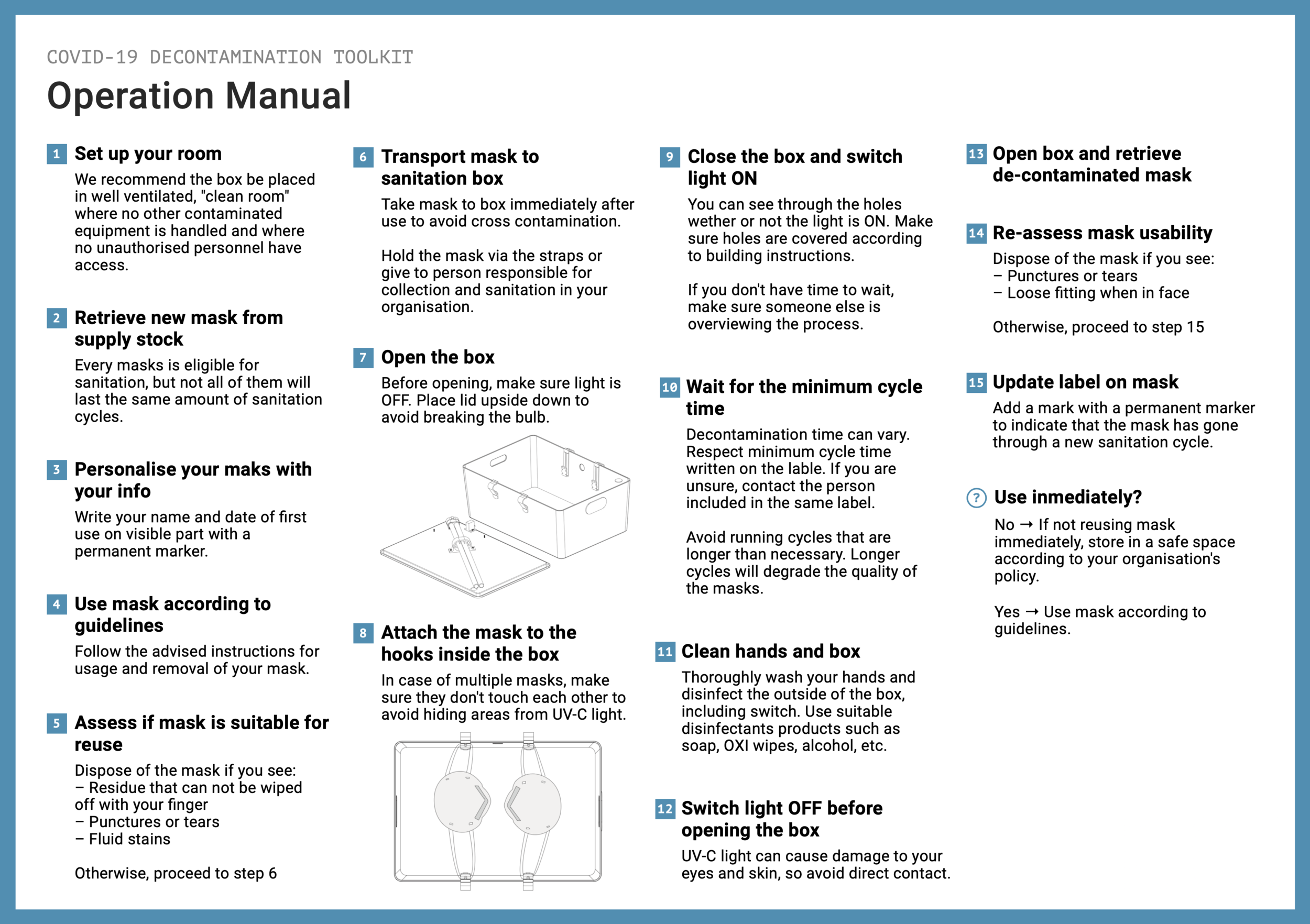
(De)centralised Coordination and Distribution
To maximise the efficiency of these kinds of design projects, the need for large scale coordination may be bigger than ever. “When it comes to healthcare, hospitals and the protection of healthcare workers, it would make perfect sense if governmental organisations were the ones taking the lead”, Pieter says. “But when we talk about everyone else that needs protective gear, it’s more kind of an open-market situation. For some, like terminally ill people or other people with vulnerable health issues, it is super important to stay protected. I would like to see some kind of centralised coordination, but it looks like it is an each-for-their-own kind of situation.” But should it be a governmental health organisation setting requirements for who gets these materials and who doesn’t? “I’m also looking at it from a more global perspective”, Pieter adds. “I’m not only making this for the Dutch market, but also for everyone else on our Earth. For every one that maybe doesn’t have the facilities to validate these kinds of approaches or the capacity to develop this. However, that is what I can do over here, after which I can share it with everyone else”.
Also Ismael and his team were looking into what their solution could offer in a non-hospital context. “Although we looked at the hospital context to gain knowledge, we are more interested in the contexts where people show up to work every day but to whom the supply of protective equipment is not funneled because the hospitals are a priority. We hope to be particularly useful in elderly care or even supermarkets, where the staff wants to stay protected for a long time but doesn’t have access to all this equipment that is made decentralised and distributed to hospitals and other emergency units”, he explains. Therefore, FROLIC wanted to make it as easy as possible for them to be responsible for their own protective gear. Hence the open-source DIY solution. “We as a studio don’t have the capacity to produce, and there is not a commercial market for our product. What we want to do is optimise the connection between demand and supply and attempt some kind of matchmaking. Fab Labs and maker spaces are great sources, but you need to make a small economic investment to produce. That’s why we think it should be demand-driven, so it could work out as a partnership.”
“You always have to take into account the local situation”, Paulien adds to the answer about responsibility. “The design capabilities and expertise are the essence and the strength of the maker community, that can happen decentralised. Particular people will step up and find ways of collaborating. However, the production needs to fit the local needs.” When it comes to design and the research plus essential and scientific knowledge needed, the maker community has already proved themselves on that part”, Paulien thinks. “Regarding distribution, we should be looking more for exciting distribution channels like the Red Cross and organisations that have direct contact with citizens in need and other healthcare organisations that are not hospitals.”
Distributed Design in a Post-pandemic World
Like Paulien said in the beginning, it’s amazing to see how fast the maker community responded to the COVID-19 crisis. “Translating the specific needs of the medical field into their models, prototypes and final products is the way to go,” she concludes. For future reference, it would be interesting to further investigate the reuse of protective materials and rethink sterilisation and decontamination, instead of continuing the production of disposables. Not only to prevent shortages in case of increasing demand but also because it is more sustainable. Protective gear is needed, but is a polluting game. To open up to these kinds of innovations, healthcare professionals also needed to experience the added value of designers and how processes are researched. Now that the scenery has changed due to COVID-19, we are met with the circumstances of a living lab, an iterative, open-innovation space to explore that real-life. As shown, distributed design opens up new opportunities and different possibilities which will hopefully influence innovative healthcare on a larger and a long-term scale, not just now.
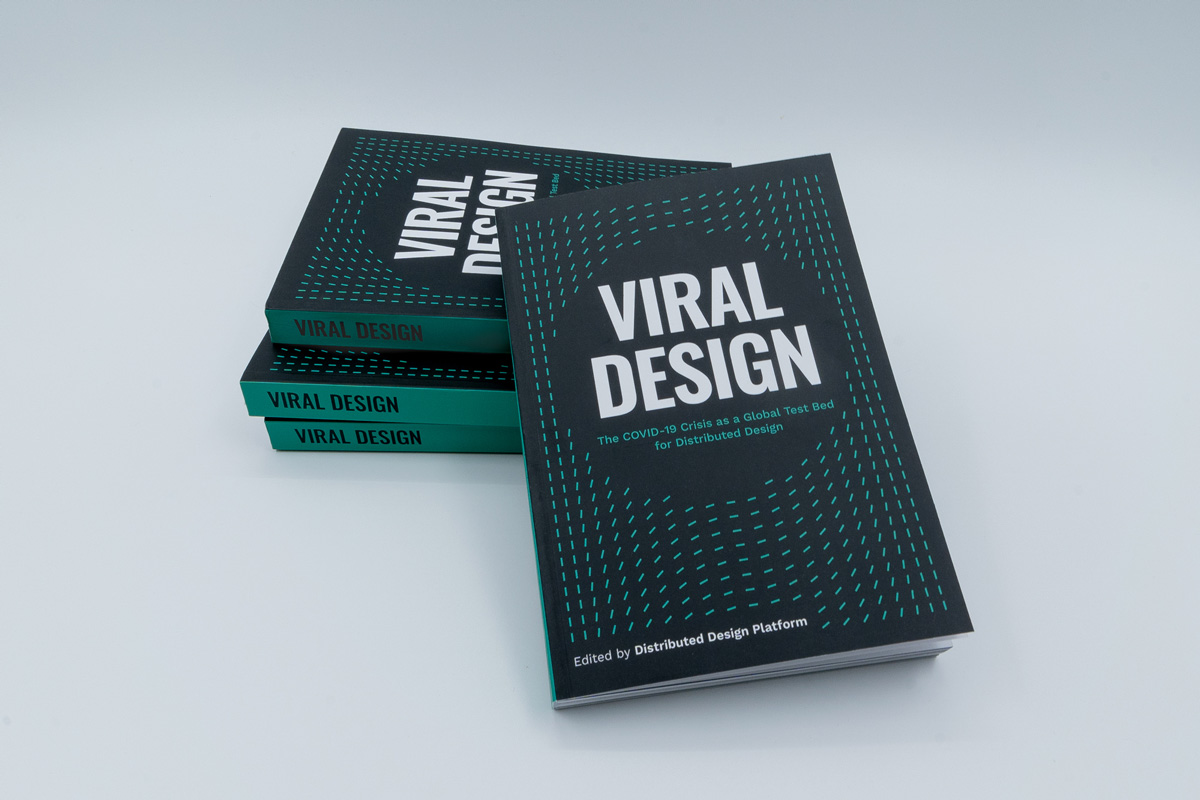